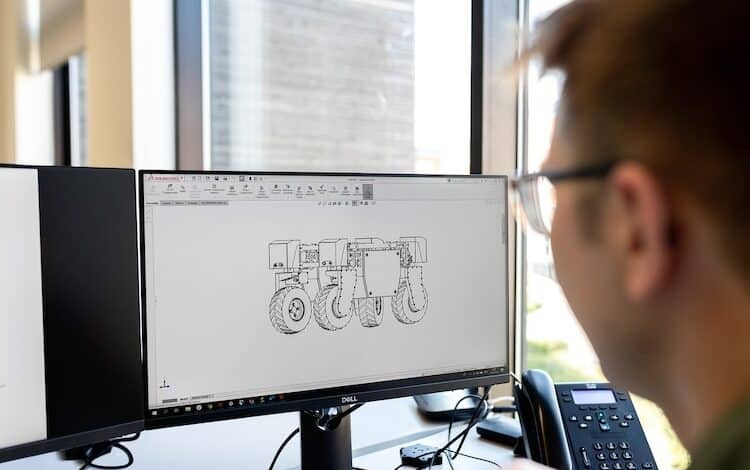
Tiefziehteile sind Bauteile, die durch das sogenannte Tiefziehverfahren aus Metall- oder Kunststoffblechen geformt werden. Dieses Verfahren ermöglicht die Herstellung komplexer, nahtloser Hohlkörper und anderer dreidimensionaler Formen aus flachen Ausgangsmaterialien. Tiefziehteile finden in zahlreichen Industrien Anwendung, darunter die Automobilindustrie, Medizintechnik, Verpackungstechnik und Elektronikfertigung. Dank ihrer hohen Präzision und Wirtschaftlichkeit sind sie aus modernen Fertigungsprozessen nicht mehr wegzudenken.
Herstellung von Tiefziehteilen
Das Tiefziehverfahren gehört zu den Umformtechniken und wird vor allem für dünnwandige Bauteile eingesetzt. Der Prozess beginnt mit einem flachen Blech, das als Rohmaterial dient. Dieses wird in eine Tiefziehpresse eingesetzt, wo es mit einem Stempel in eine Matrize gedrückt wird. Dadurch wird das Material in eine dreidimensionale Form gebracht, ohne dass dabei Material abgetragen oder verloren geht. Während des Tiefziehprozesses durchläuft das Material verschiedene Stufen der Umformung. Je nach Komplexität des Bauteils kann es erforderlich sein, mehrere Tiefziehschnitte oder Zwischenglühen durchzuführen, um die Spannungen im Material zu reduzieren. Ein entscheidender Faktor ist die Wahl der nichtigen Materialdicke und des passenden Werkstoffs. Häufig verwendetet Metalle für Tiefziehteile sind Aluminium, Edelstahl, Messing und Kupfer, während im Kunststoffbereich meist Thermoplaste wie Polypropylen oder PET eingesetzt werden.
Neben dem klassischen Tiefziehen gibt es verschiedene Sonderverfahren, die für spezielle Anwendungen genutzt werden. Dazu gehört beispielsweise das Hydroforming, bei dem anstelle eines starren Stempels eine Flüssigkeit verwendet wird, um das Material in die gewünschte Form zu bringen. Dieses Verfahren ermöglicht besonders gleichmäßige Wandstärken und komplexe Geometrien. Eine weitere Variante ist das Vakuumtiefziehen, das vor allem in der Kunststoffverarbeitung zum Einsatz kommt. Dabei wird das Material durch Unterdruck in die gewünschte Form gesaugt.
Nach dem Tiefziehen durchlaufen die Bauteile oft weitere Fertigungsschritte wie Stanzen, Schneiden oder Nachbearbeiten durch Wärmebehandlung, um die gewünschten Eigenschaften und Maßhaltigkeiten zu erreichen. Zudem werden in manchen Fällen Oberflächenveredelungen wie Lackieren, Pulverbeschichten oder Galvanisieren vorgenommen, um Korrosionsschutz oder spezielle optische Effekte zu erzielen.
Einsatzgebiet von Tiefziehteilen
Automobilindustrie
Tiefziehteile von Vogt Stanzteile sind aufgrund ihrer Vielseitigkeit in vielen Industriezweigen unverzichtbar. Ein zentrales Einsatzgebiet ist die Automobilindustrie, wo sie für Karosserieteile, Tanks, Auspuffkomponenten oder Batteriekästen verwendet werden. Dank der hohen Maßgenauigkeit und Stabilität sind sie ideal für Fahrzeugteile, die starken Belastungen ausgesetzt sind.
Medizintechnik
Auch in der Medizintechnik spielen Tiefziehteile eine wichtige Rolle. Sie werden für sterile Verpackungen von medizinischen Geräten, chirurgische Instrumente oder Gehäuse für elektrische Medizingeräte genutzt. Gerade in diesem Bereich sind präzise gefertigte Bauteile essentiell, da sie höchst hygienischen und qualitativen Anforderungen entsprechen müssen.
Verpackungsindustrie
Ein weiteres großes Anwendungsfeld ist die Verpackungsindustrie. Tiefgezogene Kunststoffverpackungen sind weit verbreitet und finden sich unter anderem bei Lebensmittelverpackungen, Blisterverpackungen für Medikamente oder technischen Produkten. Durch den Einsatz von Kunststoff-Tiefziehteilen lassen sich stabile und gleichzeitig leichte Verpackungen realisieren, die den Inhalt optimal schützen.
Elektrotechnik
Auch in der Elektronikbranche sind Tiefziehteile von großer Bedeutung. Sie kommen beispielsweise in Gehäusen für elektrische Bauteile, Steckverbindern oder Schirmungen für elektromagnetische Störungen zum Einsatz. Hier profitieren Hersteller vor allem von der Möglichkeit, passgenaue und leichtgewichtige Komponenten in hoher Stückzahl effizient zu produzieren.
Luft- und Raumfahrt
Nicht zuletzt werden Tiefziehteile in der Luft- und Raumfahrt eingesetzt, wo sie aufgrund ihrer Stabilität und Leichtigkeit für strukturelle Bauteile, Treibstofftanks oder Verkleidungsteile genutzt werden. Gerade in der Raumfahrt sind hohe Präzision und zuverlässige Fertigungsmethoden entscheidend, um den extremen Anforderungen gerecht zu werden.
Vorteile und Herausforderungen des Tiefziehverfahrens
Das Tiefziehen bietet zahlreiche Vorteile, darunter eine hohe Materialnutzung, eine gleichmäßige Wandstärkenverteilung und die Möglichkeit, komplexe Geometrien in einem einzigen Fertigungsschritt herzustellen. Es ist zudem ein wirtschaftliches Verfahren, da es sich besonders für die Serienproduktion eignet und wenig Materialverschnitt erzeugt. Die hohe Reproduzierbarkeit und Qualität machen das Verfahren attraktiv für viele Industrien.
Allerdings gibt es auch Herausforderungen. Die Wahl des richtigen Materials und die Abstimmung der Werkzeugparameter sind entscheidend, um Risse, Faltenbildung oder unerwünschte Verformungen zu vermeiden. Zudem sind die Investitionskosten für Tiefziehwerkzeug relativ hoch, weshalb sich das Verfahren vor allem für mittlere bis große Produktionsmengen lohnt. Auch das Nachbearbeiten von Tiefziehteilen kann je nach Anforderung zusätzlichen Aufwand bedeuten.