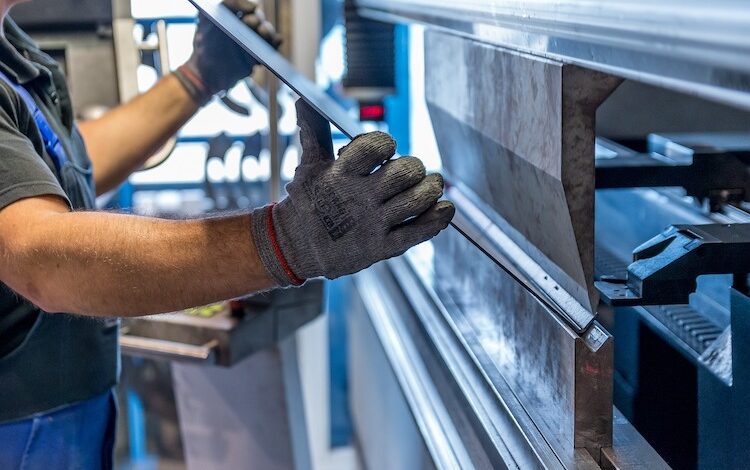
Ausfälle in der Produktion sind teuer. Dies gilt vor allem dann, wenn der Stillstand nicht geplant ist. Ob defektes Gerät oder schlechte Rohstoffplanung. Bereits die Kosten für das unbeschäftigte Personal sind Grund genug, dass viele Unternehmen ihre Produktion bestmöglich zu optimieren versuchen. Dabei braucht es nicht nur qualitative Anlagen und einen getakteten Produktionsplan. Es muss auch verstanden werden, dass Stillstände nicht unumgänglich sind.
Die Qualität von Maschinen und Anlagen ist entscheidend
Anlagen und Maschinen im Produktionsbereich sind oft teuer. Hier sollte aber dennoch in Qualität investiert werden. Die langjährige Expertise beim Pressenbau in Deutschland hilft dabei, dass Geräte möglichst hohe Laufzeiten aufweisen. Zudem werden in qualitativen Maschinen und Anlagen hochwertige Verschleißteile verbaut. Dies führt dazu, dass die Geräte einer höheren Belastung standhalten können. Zudem sind Anlagen und Maschinen von bekannten Herstellern oft bereit mit automatischer Datenanalyse ausgestattet. So lässt sich der Wartungsbedarf übersichtlich darstellen. Zu beachten ist aber auch die Verfügbarkeit von externen Technikern. Denn nicht immer kann der hauseigene Elektrotechniker die Anlage wieder in Gang setzen. Kommt es zu gravierenden Problemen, muss der Hersteller Personal entsenden. Hier sollte bereits im Zuge des Kaufs abgeklärt werden, wie schnell Techniker vor Ort sein können.
Ungeplante Stillstände vermeiden: Geplante Ausfallzeiten akzeptieren
Jede Maschine oder Anlage muss regelmäßig gewartet werden. Dies bedeutet in der Regel jedoch auch einen Stillstand. Daher gehen einige Unternehmen dazu über, diese geplanten Wartungsintervalle großzügiger auszulegen. Statt einmal im Quartal wird dann nur noch halbjährlich geprüft. Wenn geplante Ausfallzeiten jedoch vermieden werden, steigt das Risiko für ungeplante Stillstände. Ausfallzeiten zu akzeptieren, ist in der Praxis oft schwieriger als gedacht. Die regelmäßigen Wartungen können aber vom gesamten Personal sinnvoll genutzt werden. So lässt sich ein Stillstand beispielsweise mit der Reinigung der Produktionshalle oder des Außenbereichs kombinieren. Auch interne Schulungen für das Produktionspersonal können erfolgen, während Anlagen gewartet werden. Die ungeplanten Ausfallzeiten können zudem bereits jetzt schon durch diverse Sensoren in ihrer Häufigkeit reduziert werden. Dabei kommen Geräusch- und Vibrationssensoren an Maschinen und Anlagen zum Einsatz. Sobald diese einen Wert außerhalb der Norm messen, wird eine Meldung ausgelöst. Dann kann eine Wartung erfolgen, bevor das Verschleißteil ungeplant kaputt geht.
Automatisierte Prozesse beugen menschlichen Fehlern vor
Wo Menschen arbeiten, kommt es früher oder später zu Fehlern. Dabei geht es nicht darum, die Anzahl der Mitarbeiter im Produktionsbereich zu senken. Vielmehr sollten wiederholende und mühsame Aufgaben automatisiert werden. Dabei hilft es, eine langfristige Fehleranalyse zu betreiben. So wird ersichtlich, wo es häufig zu Problemen kommt. Wenn beispielsweise in einer Verpackungsmaschine Karton manuell nachgelegt werden muss, verkeilt sich dieser häufig. Hier ist es sinnvoll, auf Automatisierung zu setzen. Dann läuft der Prozess mit deutlich geringerer Fehlerquote. Ungeplante Stillstände können dann vermieden werden. Auch ein direktes Gespräch mit den Produktionsmitarbeitern kann hier Aufschluss geben. Diese wissen nämlich genau, welche Arbeiten besonders fehleranfällig oder mühselig sind. Die Automatisierung von potenziell gefährlichen und fehleranfälligen Aufgaben kann zudem auch gleich noch die Motivation der Angestellten erhöhen.